What is an LVDT?
The LVDT sensor converts the linear (or rectilinear / straight-line) movement of the object the LVDT is coupled to, into a variable corresponding electrical signal proportional to that movement.
That movement can be from as little as 0-0.5mm up to 0-1000mm in laboratory, industrial and submersible environments. See our full range of LVDTs here.
The LVDT or Linear Variable Differential Transformer is a well established electromechanical transducer design. This design has been used throughout many decades for the accurate measurement of displacement and within closed loops for the control of positioning.
How LVDTs Work – The LVDT Working Principle
So, how does an LVDT work?
In its simplest form, the LVDTs design consists of a cylindrical array of a primary and secondary winding with a separate cylindrical core which passes through the centre. (Fig A).
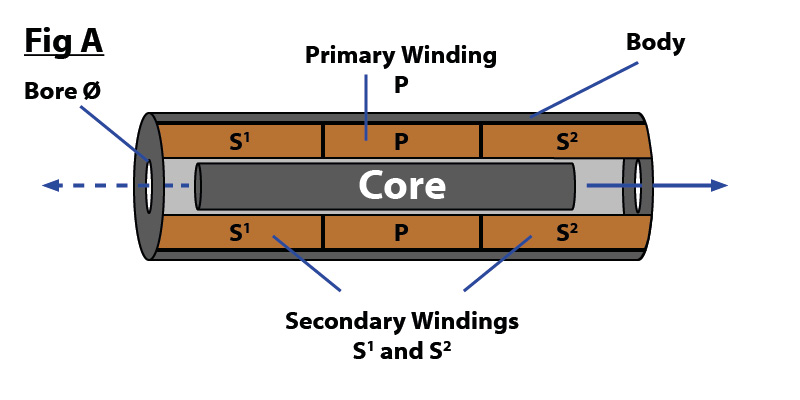
The primary windings (P) are energised with a constant amplitude A.C. supply at a frequency of 1 to 10 kHz. This produces an alternating magnetic field in the centre of the transducer which induces a signal into the secondary windings (S & S ) depending on the position of the core.
Movement of the core within this area causes the secondary signal to change (Fig B). As the two secondary windings are positioned and connected in a set arrangement (push-pull mode), when the core is positioned at the centre, a zero signal is derived.
Movement of the core from this point in either direction causes the signal to increase (Fig C). As the windings are wound in a particular precise manner, the signal output has a linear relationship with the actual mechanical movement of the core.
The secondary output signal is then processed by a phase-sensitive demodulator which is switched at the same frequency as the primary energising supply. This results in a final output which, after rectification and filtering, gives D.C. or 4-20mA output proportional to the core movement and also indicates its direction, positive or negative from the central zero point (Fig D).
Advantages of LVDT
- No Physical Contact Between the Core and the Coils
- Long Operating Life
- Theoretically Infinite Resolution
- Easy Modification
- Low Power Consumption
- High Accuracy
- Fast Response
The distinct advantage of using an LVDT displacement transducer is that the moving core does not make contact with other electrical components of the assembly, as with resistive types, as so offers high reliability and long life.
Furthermore, the core can be so aligned that an air gap exists around it, making it ideal for applications where minimum mechanical friction is required such as sensitive materials testing applications and vibration testing.
Due to the design of the LVDT displacement transducer the LVDT has a theoretically infinite resolution. However, this is limited by the LVDT instrumentation and electronics used.
LVDT Applications
The LVDT design lends itself for easy modification to fulfil a whole range of different applications in both research and industry.
Some typical variations include:-
- Complete sealing for part or full submersion in liquids and gases
- Heavy construction build for tough industrial areas – read about our industrial LVDT range
- Miniature and low cost models for price-conscious OEM usage – see our miniature lvdt range
- Internal electronic circuitry eliminating the need for additional instrumentation
Read how our industrial LVDT displacement transducer accurately monitored fabric deflection in universal fabric tension tester case study.
Speak to our expert LVDT technical team on +44 (0)118 981 7339 or email them to discuss your specific LVDT requirements.
Why Buy Your LVDT From Us?
Buy your LVDT from us, we are an expert LVDT supplier and have over 25 years of high quality LVDT supply and manufacturer experience.